PDC Cutter Performance Optimization in Drilling Operations
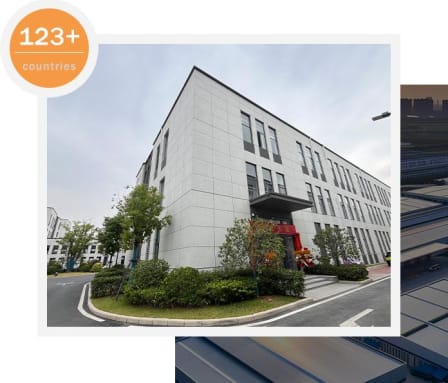
html
PDC Cutter Performance Optimization in Drilling Operations
Polycrystalline Diamond Compact (PDC) cutters have revolutionized the drilling industry with their superior wear resistance and cutting efficiency. However, optimizing their performance in drilling operations requires a deep understanding of material properties, cutter design, and operational parameters.
Key Factors Affecting PDC Cutter Performance
Several critical factors influence the effectiveness of PDC cutters in drilling applications:
- Cutter Geometry: The shape and angles of the cutter significantly impact its cutting efficiency and durability.
- Diamond Layer Quality: The microstructure and thickness of the diamond table affect wear resistance.
- Substrate Material: The tungsten carbide substrate must provide proper support to the diamond layer.
- Thermal Stability: PDC cutters must withstand high temperatures generated during drilling.
Optimization Strategies for PDC Cutters
To maximize PDC cutter performance, drilling engineers employ several optimization techniques:
1. Advanced Material Composition
Modern PDC cutters incorporate innovative diamond grain structures and binder materials to enhance toughness and thermal stability. The development of thermally stable PDC (TSP) cutters has significantly improved performance in high-temperature applications.
2. Precision Manufacturing Processes
State-of-the-art manufacturing techniques ensure consistent quality and performance across cutter batches. This includes controlled high-pressure, high-temperature (HPHT) synthesis and precise diamond table bonding.
3. Customized Cutter Designs
Tailoring cutter geometry to specific formation types can dramatically improve drilling efficiency. This includes optimizing back rake angles, chamfer designs, and cutter shapes for different rock types.
4. Operational Parameter Optimization
Matching cutter performance with appropriate drilling parameters (weight on bit, rotation speed, and hydraulics) is crucial for maximizing cutter life and penetration rates.
Keyword: cutter pdc
Future Trends in PDC Cutter Technology
The drilling industry continues to push the boundaries of PDC cutter technology with several emerging developments:
- Nanostructured diamond composites for enhanced durability
- Graded interface designs to reduce residual stresses
- Smart cutters with embedded sensors for real-time performance monitoring
- Hybrid cutter designs combining PDC and other cutting technologies
As drilling operations encounter increasingly challenging formations, the optimization of PDC cutter performance remains a critical focus area for improving drilling efficiency and reducing operational costs.