Alumina Ceramic Ball Applications and Properties
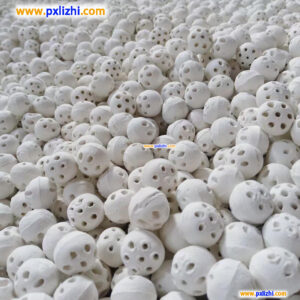
# Alumina Cerical Ball Applications and Properties
## Introduction to Alumina Ceramic Balls
Alumina ceramic balls are high-performance industrial components made from aluminum oxide (Al₂O₃). These precision-engineered spheres offer exceptional properties that make them valuable across various industries. With their unique combination of hardness, chemical resistance, and thermal stability, alumina ceramic balls have become indispensable in many applications.
## Key Properties of Alumina Ceramic Balls
### 1. Exceptional Hardness
Alumina ceramic balls rank 9 on the Mohs hardness scale, just below diamonds. This extreme hardness makes them highly resistant to wear and abrasion, significantly outperforming steel balls in many applications.
### 2. High Temperature Resistance
These ceramic balls can withstand temperatures up to 1600°C (2912°F) without losing their structural integrity, making them ideal for high-temperature environments.
### 3. Chemical Inertness
Alumina ceramic balls demonstrate excellent resistance to most acids, alkalis, and organic solvents, ensuring long-term stability in corrosive environments.
### 4. Electrical Insulation
With high dielectric strength, alumina balls serve as excellent electrical insulators in various electronic applications.
### 5. Low Density
Compared to metal balls, alumina ceramic balls have lower density (typically 3.6-3.9 g/cm³), reducing centrifugal forces in high-speed applications.
## Industrial Applications of Alumina Ceramic Balls
### Bearings and Mechanical Components
Alumina ceramic balls are widely used in precision bearings for high-speed applications where traditional steel balls would fail due to heat generation or corrosion. Their low thermal expansion coefficient ensures dimensional stability across temperature ranges.
### Grinding Media
In the mining and pigment industries, alumina ceramic balls serve as grinding media in ball mills. Their wear resistance translates to longer service life and reduced contamination compared to steel balls.
### Valve Components
The chemical inertness of alumina makes these balls ideal for use in valves handling corrosive fluids. They’re particularly valuable in the petrochemical and pharmaceutical industries.
Keyword: alumina ceramic ball
### Electronics and Semiconductors
As electrical insulators with high thermal conductivity, alumina ceramic balls find applications in electronic packaging, semiconductor manufacturing, and high-voltage equipment.
### Medical Applications
The biocompatibility of high-purity alumina ceramic balls makes them suitable for orthopedic implants and dental applications where metal sensitivity is a concern.
## Grades and Specifications
Alumina ceramic balls are available in various purity levels:
- 92% Alumina – Most economical, suitable for general applications
- 95% Alumina – Improved mechanical properties
- 99% Alumina – Highest purity for demanding applications
- 99.5% Alumina – Ultra-high purity for specialized uses
## Manufacturing Process
The production of alumina ceramic balls involves several precise steps: powder preparation, forming, sintering, and precision grinding. The sintering process typically occurs at temperatures between 1500-1700°C, creating the dense microstructure responsible for the balls’ exceptional properties.
## Advantages Over Metal Balls
Compared to traditional metal balls, alumina ceramic balls offer:
- Longer service life in abrasive environments
- Reduced maintenance requirements
- Lower energy consumption in rotating applications
- Non-magnetic properties for specialized applications
- Superior corrosion resistance
## Conclusion
Alumina ceramic balls represent a remarkable engineering solution that combines multiple superior material properties. Their unique characteristics continue to enable advancements across industries from manufacturing to medicine. As technology progresses, we can expect to see even broader applications for these versatile ceramic components.